Sailing Towards Cleaner Skies: How H.A.M. Technology Addresses NOx Pollution
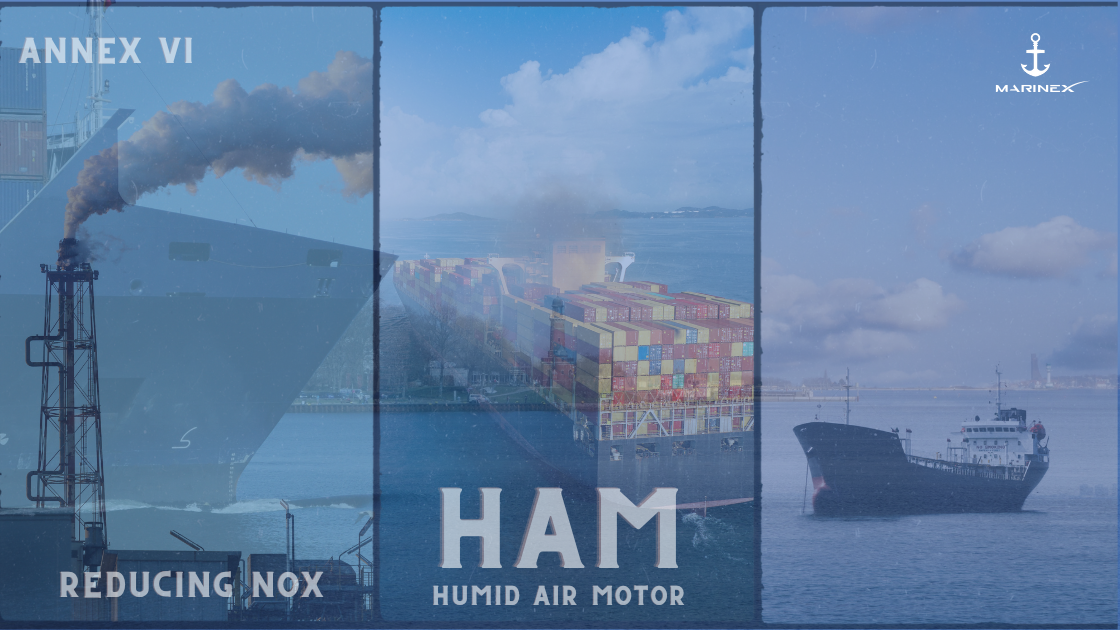
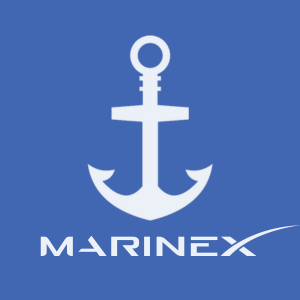
In this blog, we will be discussing how the HAM System works in reducing NOx emissions in merchant vessels. We recommend reading the entire blog for a better understanding.
Air quality improvement remains a prominent objective for engine manufacturers and users globally. Regulatory bodies are increasingly tightening emission standards to eliminate reactive pollutants from the atmosphere.
With the HAM, Humid Air Motor, the high temperature and pressurized charge air from the turbo-blower is led to the humidifier tank, named HAM vessel, where relative humidity of the air is raised to 98% with the sprayed sea water.
Meantime, the air temperature is lowered by the seawater and the air flows into the engine cylinder. The HAM system drastically curbs the NOx emission by lowering the peak flame temperature thanks to the fuel combustion with the saturated air.
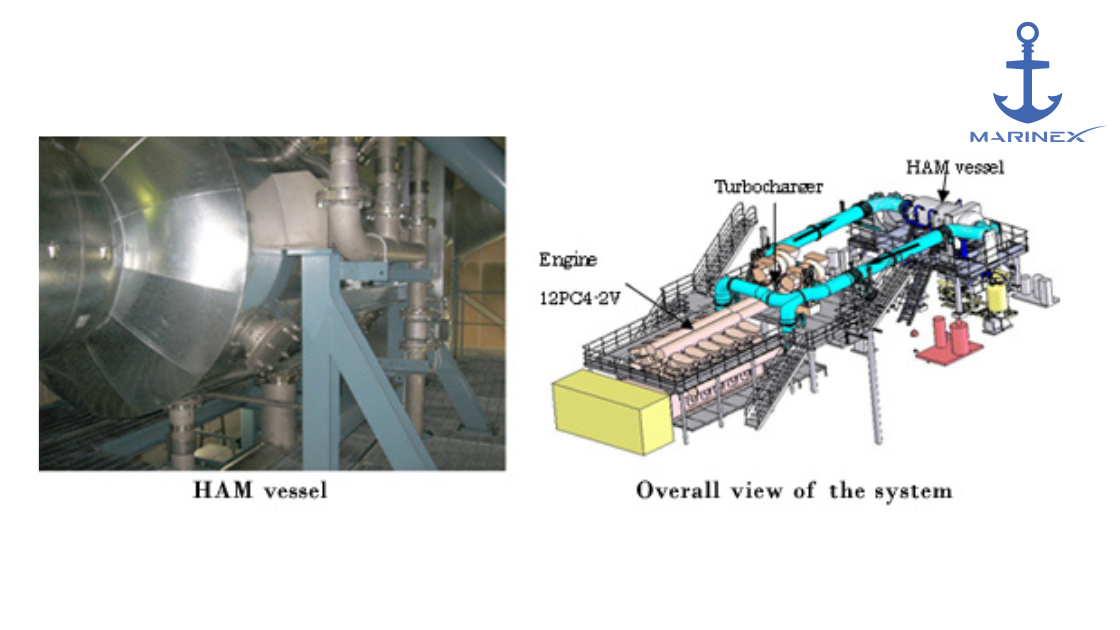
Actual results achieved show the NOx emission of about 1000 ppm through the year and some improvement in fuel consumption as the result of the engine tuning carried out at the same time.
The HAM principle addresses the issue of NOx formation, with over 90% of it attributed to combustion temperature peaks. The core idea behind HAM is to introduce humidity into the inlet air to mitigate these temperature peaks effectively.
Decoding The System
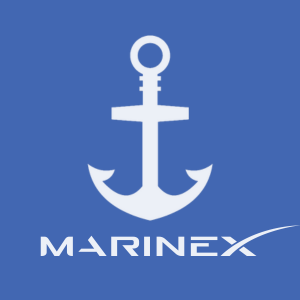
In the HAM system, a humidifier is employed to produce saturated air. This technique leverages the well-known ability of water to reduce NOx formation, akin to the concept of fuel water emulsification.
However, in the case of HAM, a significantly higher quantity of water is added, and the heat required for water vaporization is drawn from the compressed air post-turbocharger or other heat sources within the engine.
Upon the introduction of water vapor into the compressed charge air, two distinct mechanisms come into play:
- Increase in Specific Heat Capacity: The specific heat capacity of the mixture is elevated, contributing to a reduction in temperature peaks during combustion.
- Dilution of Charge Air: Water vapor replaces a portion of the air in the charge, further aiding in the reduction of temperature peaks.
The amount of water that can be injected into the inlet air (measured in grams per kilogram of dry air) depends on the temperature and pressure of the mixture.
In summary, HAM works by humidifying the inlet air, utilizing water vapor to increase the specific heat capacity of the mixture and dilute the charge air, ultimately leading to a substantial reduction in NOx emissions.
Decoding The Operational Principle
The operational principle of the Humidity Assisted Combustion (HAM) system is straightforward and can be elucidated through a sequential process. The accompanying figure provides a visual representation of the HAM process:
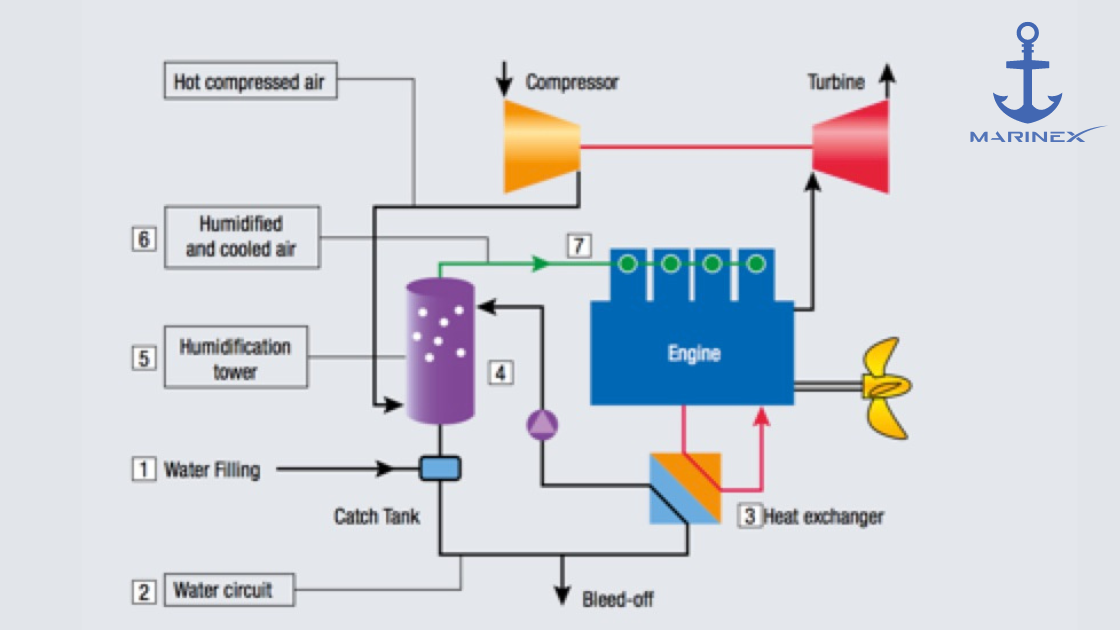
- Saltwater Filtration: Filtered saltwater is pumped into the catch tank to replenish the water lost through evaporation and purging from the loop.
- Water Circulation Loop: The HAM system operates in a closed loop, shuttling water between the catch tank and the Humidification Tower, also known as the "HAM vessel."
- Heat Exchange: A heat exchanger facilitates the transfer of heat from an on-engine heat source to warm the saltwater before it undergoes the subsequent stages.
- Three-Stage Injection: The heated saltwater is injected into the charge air through three distinct injection stages.
- Charge Air Circulation: Simultaneously, compressed charge air from the exhaust turbocharger bypasses the charge air cooler, entering the HAM vessel's air inlet. As it traverses the HAM vessel, the charge air absorbs the injected water. The high loop capacity of the water ensures that particles, including salt, are captured and redirected back into the catch tank. When the salinity exceeds a specific threshold, purging occurs, preventing any salt from entering the engine.
- Mist Catcher: To prevent tiny droplets from reaching the combustion chamber, the humidified charge air passes through a high-performance mist catcher at the end of the Humidification Tower.
- Saturated Charge Air to Engine: The humified charge air, now saturated, is directed into the engine.
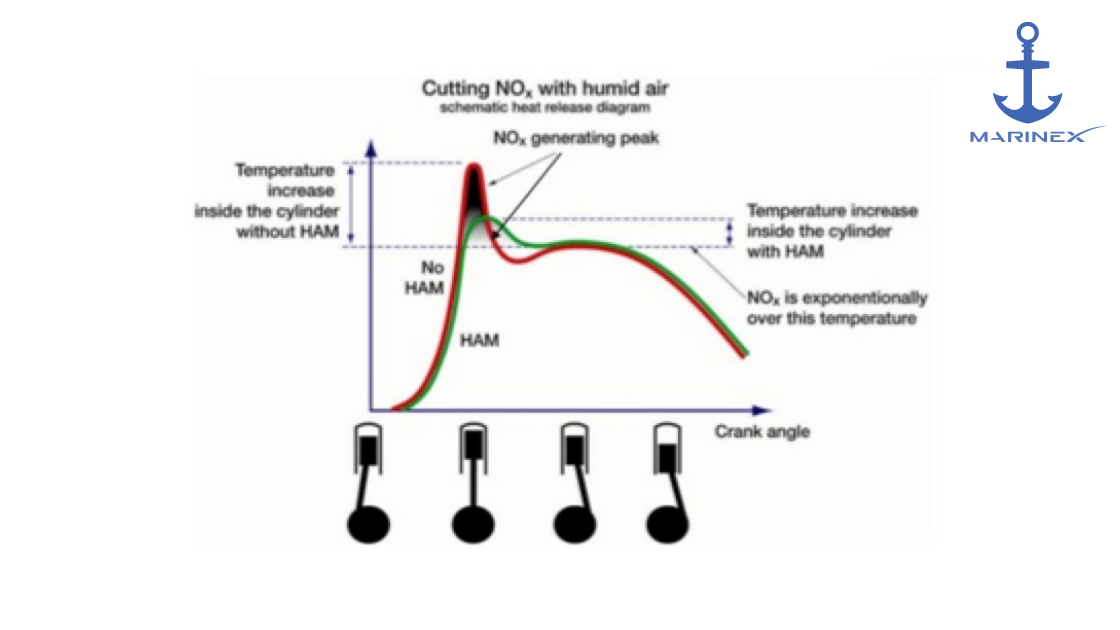
To access the full blog, subscribe to MarineX Premium Plans and elevate your maritime knowledge to the next level. Gain the MarineX Edge for comprehensive insights into all things maritime.