Ship on Blocks: Essential Maintenance Responsibilities for Chief Engineers
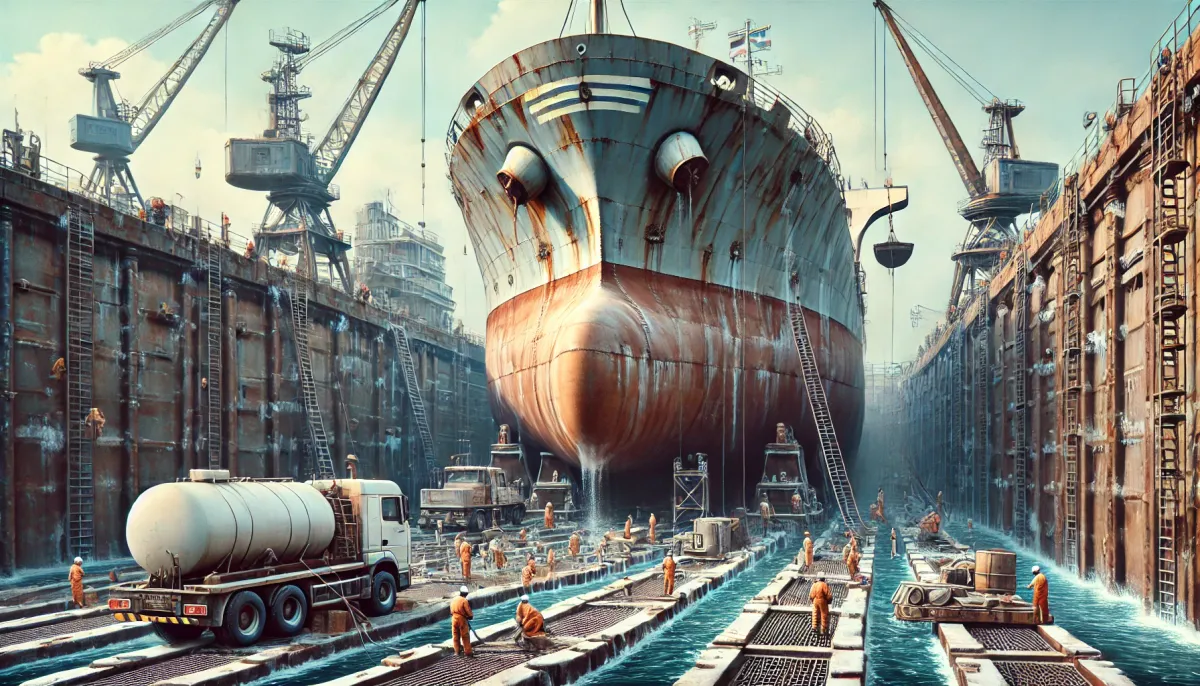
As a Chief Engineer, overseeing a vessel during drydock or when sitting on blocks requires thorough inspection and maintenance of various critical components to ensure the ship's safety, efficiency, and compliance with maritime regulations. Below is a detailed and elaborate guide covering essential actions, responsibilities, and protocols.
1. Hull Inspection for Indentation, Buckling, Corrosion, Cracks, and Adherence Points
The hull is the ship's main structural component and must be carefully inspected during drydock. The following aspects are to be examined:
- Indentation: Inspect the hull for any dents or indentations caused by external forces during the voyage. Such damage can compromise the structural integrity of the vessel and should be repaired immediately.
- Buckling: Buckling in the hull plates can occur due to pressure or stress over time. Identifying early signs of buckling is crucial to prevent catastrophic failure.
- Corrosion: Check for signs of corrosion, especially in areas exposed to saltwater. Corrosion can weaken the hull and lead to breaches. Regular maintenance and timely action can mitigate long-term damage.
- Cracks: Look for any visible cracks, particularly around joints and welded seams. These cracks can expand, leading to significant structural failure if not addressed.
- Point Adherence: Ensure the structural components of the hull adhere properly to the design specifications. Any deviations can affect the vessel's performance and safety.
2. Hull Cleaning and Repainting with Anti-Corrosive and Anti-Fouling Paints
Maintaining the hull's cleanliness and protective coatings is essential to the ship’s longevity:
- Cleaning: The hull is cleaned thoroughly to remove marine growth such as barnacles, algae, and other sea organisms. These growths increase drag, reducing the ship's fuel efficiency and speed.
- Repainting: After cleaning, the hull must be painted with anti-corrosive and anti-fouling paints. The anti-corrosive layer protects the metal from rust and saltwater damage, while the anti-fouling paint prevents marine organisms from attaching to the hull.
- Sacrificial Anodes Replacement: Sacrificial anodes, made of zinc or aluminum, help protect the hull from corrosion through electrochemical processes. These anodes corrode over time and must be replaced during every drydock to maintain their protective function.
3. Hull Damage Inspection and Repairs
Post-cleaning, the hull undergoes a detailed inspection to identify any damages that may have gone unnoticed. This includes checking for:
- Fractures and Cracks: Any cracks or fractures should be thoroughly repaired by welding and reinforcing the affected areas.
- Surface Dents: Smaller dents may need filling and refinishing to restore the hull's original form and strength.
It is important to ensure that all repairs meet safety standards and adhere to the guidelines laid out by classification societies.
4. Grating Cleaning and Overboard Valve Overhaul
Gratings, located on the sides of the ship, serve as essential drainage and water management tools. Key actions include:
- Cleaning of Gratings: Ensure all gratings are thoroughly cleaned to remove debris, dirt, or corrosion, which could obstruct water flow.
- Repairing Gratings: Any damage to the gratings is to be repaired to maintain their functionality.
- Overboard and Sea Suction Valves Overhaul: All valves related to overboard discharge and sea suction must be overhauled. Over time, these valves can develop leaks or faults, compromising the ship's seaworthiness. Regular overhauls ensure optimal operation.
5. Inspection and Cleaning of Tanks Below Water Level
Tanks situated below the waterline, such as water ballast tanks, fuel tanks, and freshwater tanks, require special attention due to their critical functions. The steps include:
- Gas-Freeing: Before any inspection, tanks must be made gas-free to eliminate hazardous vapors. This ensures a safe environment for workers entering the tank.
- Man Entry Permit: Before personnel enter the tanks, a man entry permit must be secured to ensure all safety measures are in place.
- Internal Cleaning: All tanks must be internally cleaned to remove any accumulated sludge, sediments, or contaminants that could affect the tanks' function and integrity.
- Hot Work Permits and Risk Assessment (R.A.): If any repairs are necessary, additional permits for hot work must be obtained, along with a comprehensive risk assessment to ensure the safety of the workers.